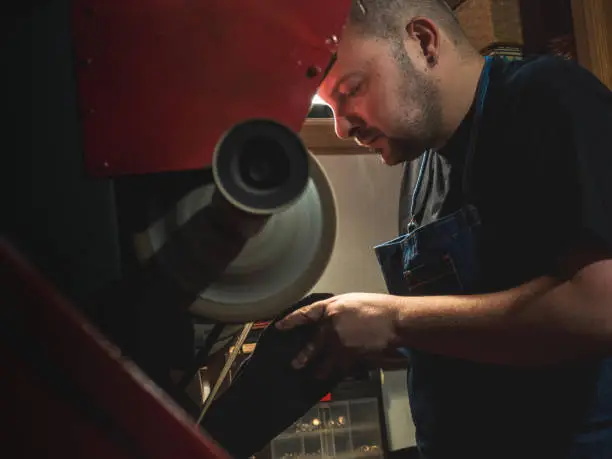
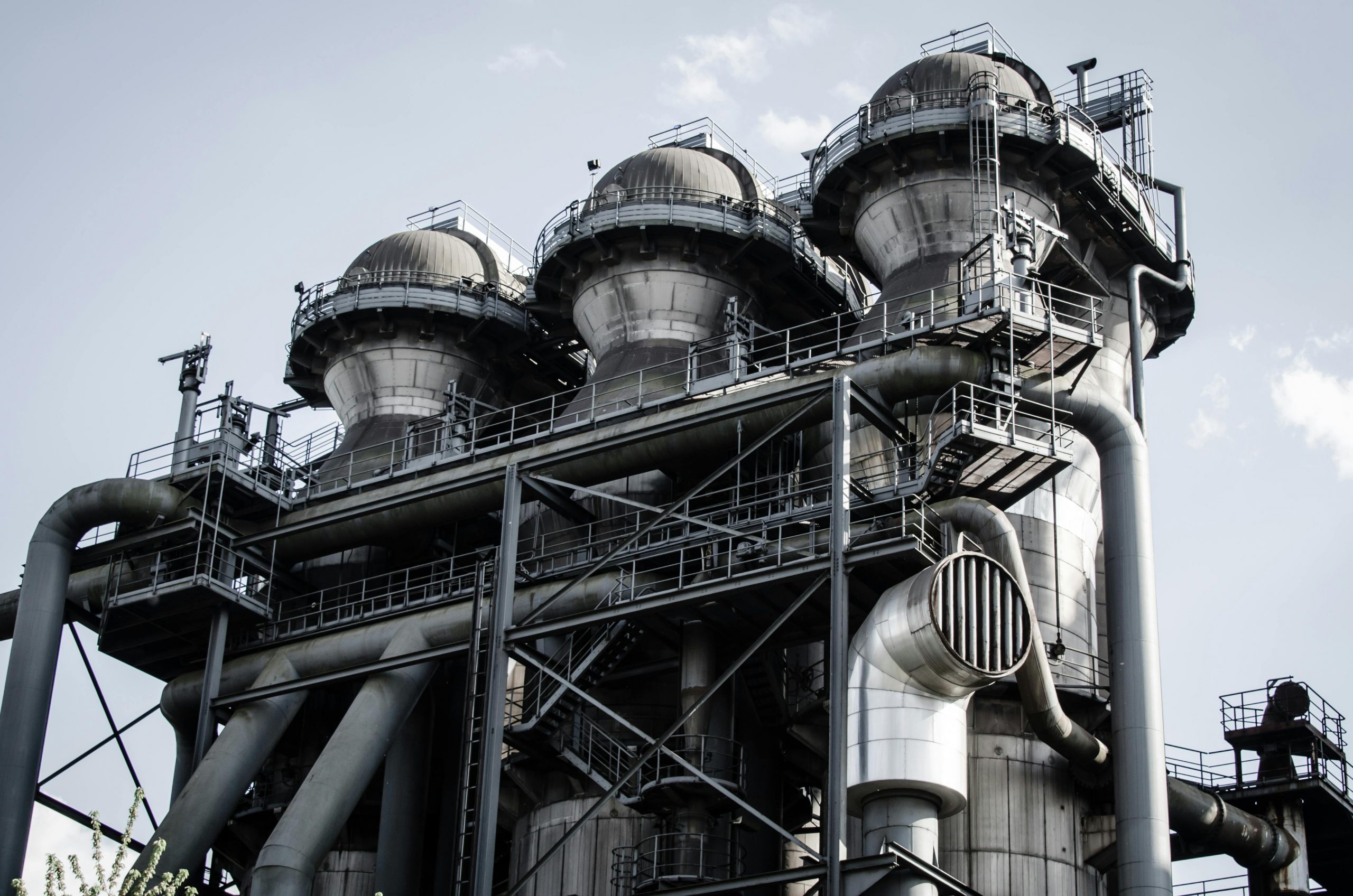
Choosing the right materials for pressure vessels
Nowadays, there are countless industrial processes that rely on pressure vessels to function. Businesses that have been operating in these fields might have a good idea of what materials these essential components should be made from. That being said, there are always new developments in working practices and techniques in metal forming. In this article, we’ve used our specialist materials knowledge to provide valuable recommendations on the best materials for pressure vessels.
Uses for pressure vessels
Pressure vessels are some of the most ubiquitous metal spun parts out there, able to be used by a variety of manufacturing businesses to support key processes. A good example is the chemical and food industry, along with a wide range of technical research industries. A boiler pressure vessel is also commonplace in most residential and commercial buildings to provide heating.
In these industries and many others, pressure vessels perform a vital role in storing pressurised liquids and gases. As a result, it’s important that these parts are made from materials that can withstand pressures well above ambient levels. This enables the pressure vessel to perform its function and avoids integrity failures such as buckling, fracture, overload, or another form of deformation.
Material properties for pressure vessels
As is the case for any component or metal spun part, the material it’s made from plays a big role in the properties it takes on. However, there are certain properties that must be prioritised when choosing which material to use for pressure vessels.
One of the key statistics of pressure vessels is their maximum allowable working pressure (MAWP). This figure, along with the maximum design temperature, make up the conditions that the pressure vessel should be. A pressure vessel that can’t handle the temperatures and pressures necessary for its intended function will produce substandard and dangerous results. As such, materials need to be chosen in consideration of the conditions of the pressure vessel, along with the substances kept inside.
The material that makes up a pressure vessel must be strong enough to withstand force without damage or distortion. The exact degree of load and the type of stress will depend on the processes it is required for. At Tanfield, we are experienced in generating material recommendations based on the component and your unique application.
Pressure vessels are typically used to store liquids and gases that are volatile or generally unsafe for workers. Therefore, metal parts for pressure vessels must be made from a corrosion resistant material for longevity, reliability, and to uphold worker safety.
In addition to corrosion, there are other external factors which can impact the performance of a pressure vessel. This factor is especially prevalent in pressure vessels that are positioned in an outside environment. Here, extra care must be taken in the construction of the vessel to ensure seals remain intact and leaks don’t appear. For instance, any dished ends for pressure vessels are best made from an easily weldable material.
Recommended materials for pressure vessels
If you require pressure vessels to facilitate a project or industrial process, you should consider if the following materials will meet your needs:
- Steel – this is a common material throughout industrial facilities due to its strength and heat resistance. Steel also has a high tensible strength, which makes it ideal to be subjected to cold forming processes, such as metal spinning, without breaking.
- Stainless steel – specific grades of stainless steel are better suited for pressure vessels due to their corrosion resistance. Stainless steel 316 is widely regarded as having the highest resistance to corrosion out of all the stainless steel grades.
- Duplex – these variants of stainless steel are known for their even higher strength, which is due to the micro structures within the metal. Although duplex is more difficult to fabricate as a result.
- Nickel – well suited to withstanding thermal expansion forces which can often occur within pressure vessels.
- Aluminium – high tensile strength relative to weight, although not well suited to extremes in temperature and pressure.
- Titanium – low conductivity and density, combined with high ductility. It is also the strongest metal relative to its density, so titanium pressure vessels can save space even if they’re usually more expensive.
- Hastelloy – an alloy of nickel with amounts of chromium and molybdenum, Hastelloy has a very high resistance to temperature and corrosion.
Materials specialists in manufacturing
The team at Tanfield Metal Spinners possesses extensive knowledge in cold forming techniques. We’ve seen first-hand prototypes buckle and fail under the stresses and strains of high temperature and pressure. This is a standard part of our pressure vessel testing process, along with quality control checks focused on precision. Our forming capabilities for pressure vessels are among our most considerable, with Tanfield technicians able to spin a wide range of materials to meet our client’s needs. Get in touch and we’ll be happy to draw up a quote.